Проектирование пресс-форм
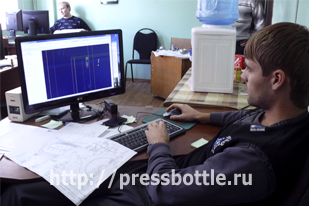
Проектирование пресс – форм
-
Разработка техпроцесса литья
-
Построение формообразующих
-
Выбор блока и формообразующих
-
Проектирование системы охлаждения
-
Проектирование системы съема
-
Проектирование и крепление элементов
-
Оформление конструкторской документации
Во время разработки техпроцесса литься конструктор, основываясь на сложностях изготавливаемого изделия определяет силу смыкания формы, время одного цикла и количество мест в форме.
В зависимости от метода доставки материала в формующую полость, пресс-формы можно разделить:
Холодноканальные – формы, находясь в которых литник охлаждается и затвердевает, после чего выталкивается изделиями в каждом цикле литья.
Основным достоинством ХКС является их простота, так как в них отсутствуют терморегуляторы и нагреватели. В результате получается, что проектирование пресс-форм с такой литниковой системой обходится гораздо дешевле.
Основной недостаток – требуется отделять застывший разводящий литник.
Среди холодноканальных существуют формы как с двумя плитами, так и с тремя.
Горячеканальные – формы, в которых разводящий литник остается в расплавленном состоянии и его не требуется извлекать во время цикла литья. Распределение горячеканальных форм является более трудным. Как правило, в описании присутствуют два главных элемента – сопла и коллекторы. Данные элементы бывают теплоотводящие, нагреваемые или изолированные.
К основному преимуществу относится отсутствие разводящих литников, из-за чего уменьшается литьевой цикл.
Основной недостаток – высокая цена и сложность производства ГКС.
Конструкция ГКС является аналогичной ХКС формы, имеющей три плиты: благодаря расположению центрального литникого канала есть возможность замены места впрыска материала.
В состав ГКС входит два главных элемента: система сопел и коллекторы. Благодаря коллектору, находящемуся внутри полуформы матриц, осуществляется доставка расплава из сопла литьевой машины в нужные места, после чего при помощи сопла обеспечивается прохождение расплава в формующую полость из коллектора.
После того, как осуществлен выбор доставки материала до формообразующей полости, конструктор определяется с выбором количества гнезд в форме.
Гнездо – это деталь формообразующей полости, благодаря которой осуществляется отлив одной детали. В результате получается, что за один цикл можно создать сразу несколько элементов. Количество гнезд в форме определяется в зависимости от сложности изделия, его габаритов. Использование многоместных форм целесообразно для многих малогабаритных элементов, так как при этом в несколько раз увеличивается производительность пресс-формы при ее небольшом увеличении в цене.
После этого конструктор занимается определением усилия смыкания формы и времени одного цикла. Для этого ему требуется тщательно продумать форму изготавливаемой детали и создать такие условия, в результате которых материал заполнит всю формообразующую полость за наиболее короткое время.
Построение формообразующих.
К формообразующим относят все элементы, которые соприкасаются с отливкой: пуансон, матрица, резьбовые знаки, гладкие знаки и прочее.
Когда осуществляется проектирование пресс-формы, требуется сводить к минимуму поднутрения в отливаемом изделии. Поднутрениями называются узкие полости, разнообразные выемки и пазы в отливаемом изделии, которые затрудняют литье и формовку. В результате, появляются различные технологические трудности и брак в производстве.
Выбор блока и размещение в нем формообразующих.
После того, как завершено построение формообразующих, выбирают блок, подходящий для их размещения. Это зависит от габаритов формообразующих, параметров литьевой машины и прочего.
Проектирование системы охлаждения.
Как правило, по усмотрению конструктора-проектировщика, в систему охлаждения входят прямые, спиральные или кольцевые каналы для охлаждающей жидкости. Как правило, в этом случае обычно используется специально подготовленная термостатированная вода, реже – раствор гликоля. В большинстве случаев, в пресс-форме находится несколько охлаждающих контуров, хотя, для необходимой работы бывает достаточно и одного. Охлаждающая жидкость, находящая в каждом из контуров, обладает своей температурой, отличной от остальных.
Проектирование системы съема.
Системы для съема изготовленных изделий делятся на две категории: механические и пневматические. В первом случае – пружины приводят в действие выталкивающие стержни, во втором – эту работу выполняет сжатый воздух. В некоторых случаях, когда изготавливаемая деталь обладает наиболее сложной формой, извлечение изделий из формы происходит вручную.
Проектирование системы крепления и транспортных элементов.
На данном этапе происходит разработка системы крепления пресс-формы в литьевой машине. Помимо этого, происходит проектировка приспособлений, которые облегчают транспортировку пресс-формы. Это требуется потому, что вес пресс-формы варьируется в пределах от 0,1 до 3,5 тонн.
Оформление конструкторской документации.
Во время проектирования пресс-формы, конструктор, как правило, пользуется средствами трехмерного моделирования. Благодаря этому можно не только сэкономить время за счет автоматизации процессов и применения в проектировании уже готовых стандартных деталей, но, так же, по завершении работ, получить полностью готовую трехмерную модель пресс-формы. Благодаря такому подходу облегчается правильность проектирования отдельных деталей, проверка собираемости, как отдельных систем, так и полностью готовой пресс-формы.